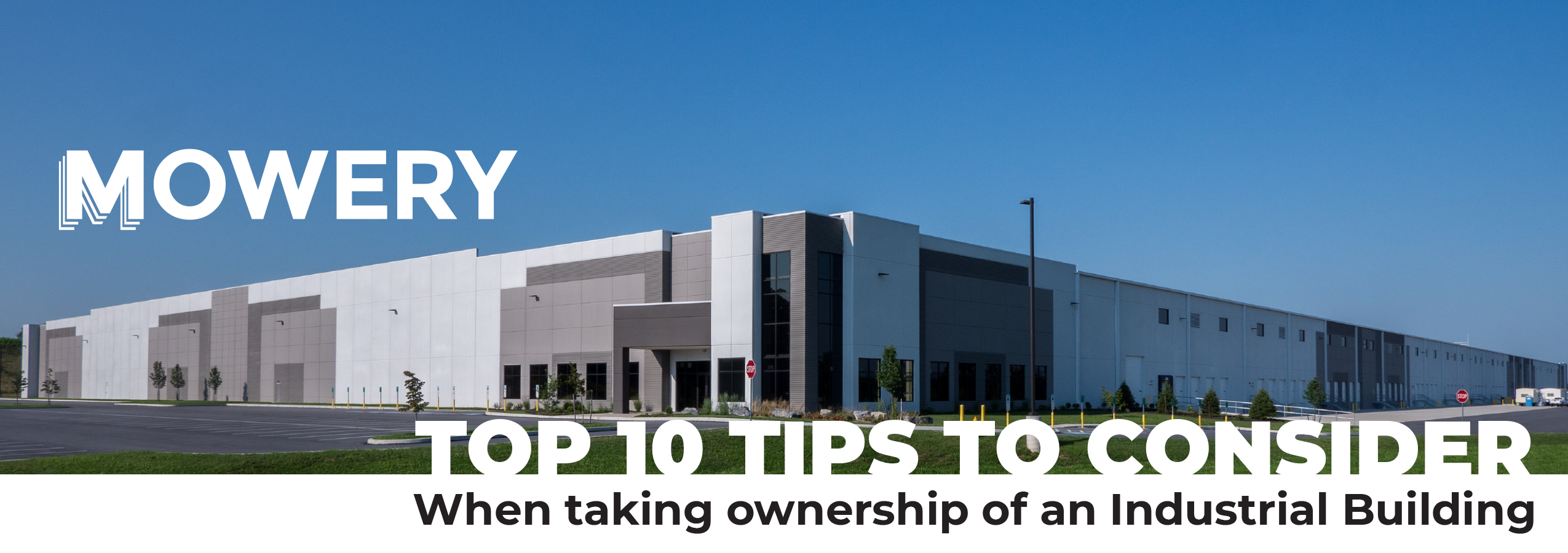
Top 10 Tips to Extending the Performance of an Industrial Building
by September 28, 2018 | News |
|Over the years, Mowery has built over 25 million square feet of industrial projects. While each project included different teams, designs, materials, clients and tenants, the buildings and the relationships created through a remarkable experience are testaments to what “For the Experience” represents.
At Mowery, we want each new building to perform to the standards expected by the owner and their tenants long after the building is finished. To help achieve this goal, below are a list of the top 10 items critical to ensure a new building stays good as new, for as long as possible.
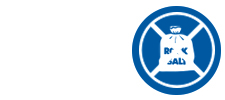
Protect Concrete
Although most concrete cures in seven days, keeping chemicals and deicers off the surface for at least 12 months is critical to avoid deterioration and surface failures. If you must apply materials to the concrete for ice or snow removal, use plain cat litter instead of chemicals. Lots of snow? Get out the shovels and remove it the old-fashioned way – with a little manpower.
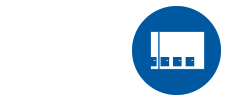
Regularly Maintain Dock Equipment
Dock equipment can be an expensive investment for an industrial complex. So when the equipment fails, it could lead to big-ticket repair costs. Remember to exercise dock equipment monthly and lubricate per the manufacturers recommendations to avoid expenses down the road.
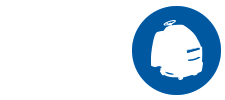
Invest in a Scrubber Dump
Using a commercial floor scrubber is a standard method to clean large industrial complexes. While these machines provide efficiencies from a cleaning perspective, they also create gallons of dirty liquids. If not properly disposed of, this liquid can cause havoc on plumbing systems and can even be harmful to workers and the environment. Having a scrubber dump can alleviate these issues.
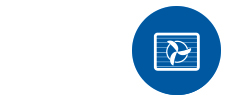
Keep the Air Moving
Ventilation systems not only bring fresh air indoors and remove contaminated air, they also help building materials such as concrete fully cure. Whether occupied or not, air handling units should run regularly in new and even existing buildings.
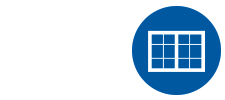
Reduce Window Pain
Windows installed on commercial and industrial buildings are often designed to create energy efficiencies providing long-term utility savings for owners. While it may be tempting to alter the windows with blinds affixed to the frames or painting the glass to provide shade or reduce glare, those changes can affect the efficiency of the window. Consider other options first for windows such as manufacturer-approved window treatments and glare solutions. Additionally, regularly inspect windows for cracks or breaks as well as how the sealant is performing will also keep down costs.
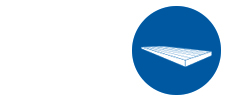
Keep Up with Rooftop Maintenance
No matter the element – wind, snow, rain or heat – the roof is always exposed and can make it the most vulnerable part of a building’s exterior. To ensure the roof performs as intended in the initial design, keep gutters and drainage systems clear always. Plus, when accessing the roof, use slip sheets or extra roofing material to protect the roof from foot traffic and/or heavy loads of other materials.
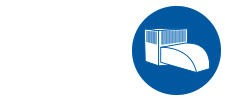
TLC for the HVAC
Facility costs account for a large percentage of operating expenses for industrial building owners. Lowering energy costs can impact the bottom line and a properly maintained HVAC system is a good first place to start. Using proper manufacturer-recommended filters and changing them based on the recommended durations ensures maximum efficiency and air quality. Plus, remember to inspect and clean coils and cables and clear drain pans and condensation lines of obstructions. A routine professional inspection by a third-party vendor is also recommended.
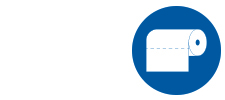
Limit Paper Towel Usage
It may be hard to believe, but paper towels often make their way to unwanted places (like toilets and drains) and can lead to pipe blockage issues. Consider purchasing commercial products that are easily degradable to prevent clogs and issues (in case they are not properly disposed of). Remember while avoiding paper products completely may not be feasible, having trash cans accessible in areas like bathrooms, kitchens and public spaces will make disposal easier.
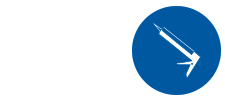
Use the Correct Caulk
Caulking seals joints or seams in structures and/or around piping. Over the course of months (or years) as a building settles, caulking may be necessary to seal small gaps to protect structures against water, air, dust or other components. Remember to use the proper caulking material for the job as there are several different varieties including paintable vs. non-paintable and expandable vs. shrink resistant.
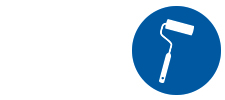
Touch Up Paint
Commercial-grade paint not only offers curb appeal, but also can protect materials such as wood from the elements. Remember, commercial paint usually has a life span of five years; however, it may be shorter due to exposure or even the color selected (i.e. vibrant and dark colors, for example, often have a shorter life expectancy than neutral colors). It’s good practice to inspect trim and surfaces after 3-4 years to gauge whether a fresh coat of paint is required.
Are you interested in learning more about how Mowery partners with its clients on industrial projects? Contact us today! At Mowery, we work collaboratively with our partners, during both the preconstruction and construction phases, through a proactive approach known as our PARTNER Program. The goal of the PARTNER Program is to create not only a unique and custom experience for our clients, but a remarkable one as well. This is truly how we measure success — and the experience we provide for our clients has made us the contractor-of-choice for local, regional and national companies.